Specialty Services
Elastomeric Waterproofing
Elastomeric waterproofing is a 100% solids, two part polyurea. The material is applied through the use of a plural component high pressure pump to provide a seamless waterproofing system.Â
Concrete substrates are prepped by media blasting to remove any contaminants and provide a better profile for adhesion. The primer is then applied with a plural component pump and allowed to become tack free. The membrane is applied at a nominal 80mils over the primer. The material has a gel time of roughly 5 seconds. On bridge decks that will receive an asphalt overlay a second layer of membrane is applied at 30-40mils with aggregate broadcast into the material to provide a shear-key. The top coat material has a slightly longer gel time of 30-40 seconds to allow for the aggregate to be broadcast. After a cure time of 1-hour the membrane system can be opened to light traffic for up to 7-days or can be paved across. A tack coat of performance grade asphalt is applied prior to overlaying with asphalt.
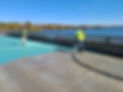

Epoxy Overlay
Epoxy overlays consist of a moisture-insensitive, 100% solids, low-modulus epoxy urethane co-polymer resin and an angular highly siliceous metamorphic or igneous rock greater than 7 on the Mohs Hardness Scale.
Concrete substrates are prepped by media blasting to remove any contaminants and provide a better profile for adhesion. The epoxy material is dispensed through the use of a two component 1:1 ratio pump. The material is squeegeed with the use of a grooved squeegee onto the bridge deck at a coverage rate of 40sf/gal. The aggregate is then broadcast into the epoxy until refusal roughly 15lbs/sy. The epoxy is allowed to cure, cure times depend on material, surface, and ambient temperatures. After the epoxy is cured the excess aggregate is swept from the surface. A second coat is then applied similar to the first coat with coverage rates of 20sf/gal for the epoxy and 25lbs/sy for the aggregate. The second coat is cured and then the loose aggregate is again swept from the surface. Traffic can be allowed on the overlay after the aggregate is swept from the second coat.

Polyester Polymer Concrete (PPC):
PPC consists of an isophthalic polyester-styrene co-polymer resin, natural sand, and aggregate greater than 7 on the Mohs Hardness Scale.
Concrete substrates are prepped by media blasting for an overlay and by removing unsound concrete and media blasting for patching. A High Molecular Weight Methacrylate (HMWM) primer is applied to any horizontal or vertical surface that is to receive the PPC by utilizing brooms, rollers, or brushes. Resin is then mixed with the initiator and accelerator, if needed depending on temperature, and dumped into a mortar mixer. The sand and aggregate is then added to the mortar mixer in the appropriate ratios and allowed to mix for 2 minutes. PPC is then dumped into a wheel barrow and taken to the placement location. The PPC is finished to grade by the use of a vibratory screed and/or standard hand finishing tools depending on the size of the overlay/patch. After finishing, a top sand is applied to cover any surface resin. The overlay/patch can then be tined or mechanically textured after curing. PPC has a rapid cure time and in most instances can be safely returned to traffic within 2 hours. PPC can be placed in overlays from ¾” to 12” thick in a single lift and can be placed in patches in variable thickness.
Asphaltic Plug Dams
Asphaltic plug dams consist of a hot applied polymer modified asphalt binder and specially selected and processed aggregate.
Existing joint of asphalt is saw cut and removed to the width specified. The asphalt binder is heated in a double jacketed hot asphalt kettle to the temperature range specified. The aggregate is placed in a rotating drum mixer and heated to the temperature specified with a hot air lance or torch. Once both materials are heated to their respective temperatures the asphalt binder and aggregate are mixed together at a ratio of 1-gal of binder per 50-lb bag of aggregate. The binder aggregate mixture is then placed in the prepared joint in lifts up to 3”. After the final lift is placed the joint is compacted with a roller or vibratory plate compactor. Binder is applied to the top surface to fill in any voids and a dress aggregate is applied to cover the binder. Traffic can be placed on the joint after it has properly cured, times depend on the depth of the joint and ambient temperatures.
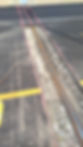
High Friction Surface Treatment (HFST)
HFST consists of a moisture-insensitive, low-modulus, high friction surface polymer resin and a high-friction bauxite aggregate.
Asphalt pavement is cleaned with mechanical sweepers and high pressure air. Concrete pavement is cleaned by media blasting. The resin material is dispensed through the use of a two component 1:1 ratio pump. The material is squeegeed with the use of a grooved squeegee onto the pavement at a coverage rate of 25-32 sf/gal. The aggregate is then broadcast into the resin until refusal at a rate of 12-15lbs/sy. The resin is allowed to cure, cure times depend on material, surface, and ambient temperatures. After the resin is cured excess aggregate is swept from the surface. Traffic can be allowed on the overlay after the aggregate is swept.
